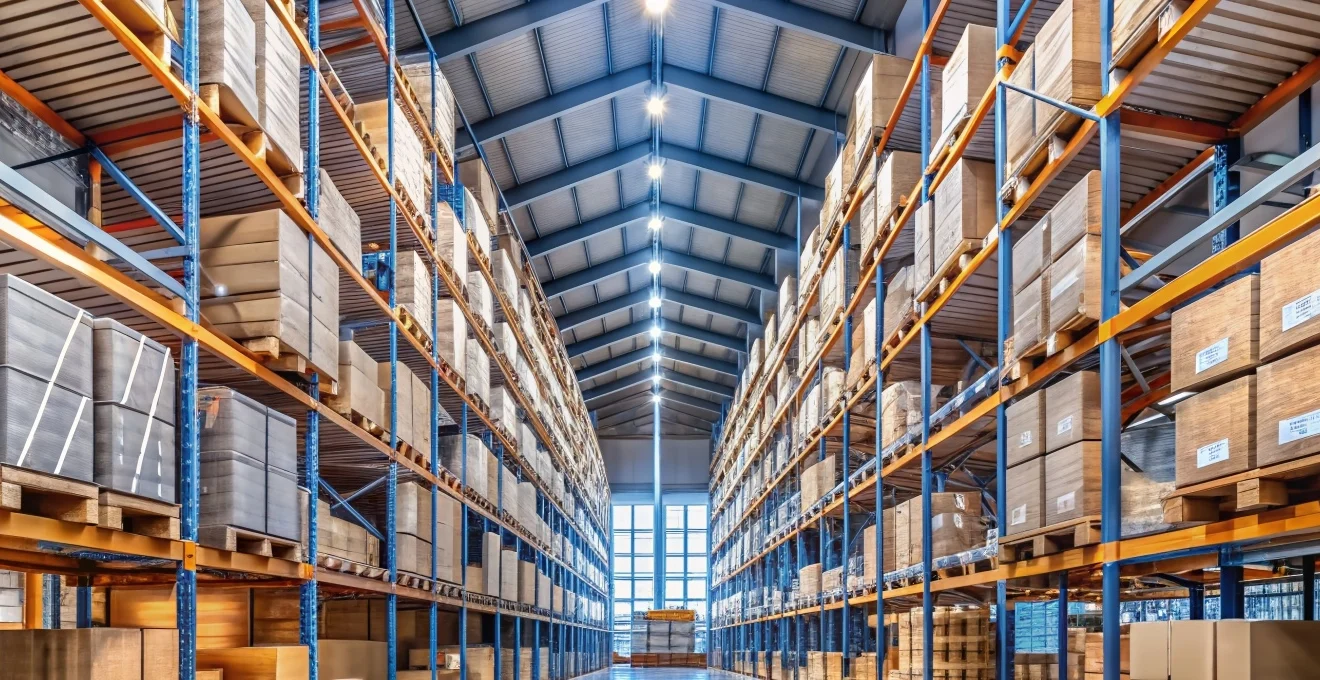
L’optimisation de l’espace de stockage est un enjeu crucial pour toute entreprise gérant un entrepôt. Un rayonnage bien conçu et adapté à vos besoins spécifiques peut révolutionner votre organisation logistique, augmenter votre productivité et réduire vos coûts opérationnels. Que vous gériez un petit entrepôt ou un vaste centre de distribution, le choix judicieux de vos systèmes de rayonnage peut faire toute la différence. Découvrez comment transformer votre espace de stockage en un outil stratégique pour votre entreprise.
Types de rayonnages industriels pour optimiser l’espace d’entreposage
Le choix du bon système de rayonnage est la pierre angulaire d’un entrepôt efficace. Il existe une multitude de solutions adaptées à différents types de marchandises et de flux logistiques. L’objectif est de maximiser l’utilisation de l’espace tout en facilitant l’accès aux produits stockés. Veuillez consulter ce site spécialisé pour découvrir les principales options qui s’offrent à vous pour optimiser votre espace d’entreposage.
Rayonnages à palettes : capacité de charge et flexibilité
Les rayonnages à palettes sont la solution la plus courante dans les entrepôts industriels. Ils offrent une grande capacité de charge et une flexibilité remarquable. Ces systèmes peuvent être configurés pour accueillir des charges allant de quelques centaines de kilos à plusieurs tonnes par niveau. La modularité des rayonnages à palettes permet de s’adapter à différentes tailles de palettes et de modifier facilement la configuration en fonction de l’évolution de vos besoins.
Un avantage majeur des rayonnages à palettes est leur accessibilité directe à chaque palette stockée. Cela facilite la gestion des stocks selon le principe du FIFO (First In, First Out) et permet une rotation efficace des produits. Pour une utilisation optimale, il est crucial de choisir la profondeur et la hauteur adaptées à vos produits et à la configuration de votre entrepôt.
Systèmes de stockage dynamique : FIFO et LIFO
Les systèmes de stockage dynamique offrent une solution innovante pour maximiser la densité de stockage tout en assurant une rotation efficace des stocks. Il existe deux principales configurations : le FIFO (First In, First Out) et le LIFO (Last In, First Out).
Le système FIFO utilise des rayonnages à gravité, où les palettes sont chargées d’un côté et se déplacent automatiquement vers l’avant grâce à des rouleaux inclinés. Cette configuration est idéale pour les produits avec une date de péremption, car elle assure que les produits les plus anciens sont toujours accessibles en premier.
Le système LIFO, quant à lui, est adapté aux espaces plus restreints. Les palettes sont chargées et déchargées du même côté, ce qui convient parfaitement aux produits non périssables ou aux stocks tampons. Ces systèmes permettent d’optimiser l’utilisation de l’espace en réduisant considérablement les allées nécessaires.
Rayonnages cantilever pour charges longues et irrégulières
Pour le stockage de charges longues ou de formes irrégulières, les rayonnages cantilever sont la solution idéale. Ces structures, caractérisées par des bras en porte-à-faux fixés à des colonnes verticales, sont parfaitement adaptées pour stocker des tubes, des profilés, des planches ou tout autre matériau de grande longueur.
L’avantage principal des rayonnages cantilever réside dans leur flexibilité d’utilisation . Les bras peuvent être ajustés en hauteur et en profondeur pour s’adapter à différentes tailles de produits. De plus, l’absence de montants frontaux permet un accès facile aux marchandises, facilitant ainsi les opérations de chargement et de déchargement avec des chariots élévateurs.
Pour optimiser l’utilisation des rayonnages cantilever, il est recommandé de :
- Classer les produits par longueur et poids pour faciliter leur manipulation
- Utiliser des séparateurs entre les bras pour organiser différents types de produits
- Prévoir un espace suffisant entre les rangées pour manœuvrer en toute sécurité
Mezzanines de stockage : exploitation verticale de l’espace
Les mezzanines de stockage représentent une solution ingénieuse pour exploiter la hauteur souvent sous-utilisée des entrepôts. En créant un ou plusieurs niveaux supplémentaires, vous pouvez doubler ou tripler votre surface de stockage sans augmenter l’emprise au sol de votre bâtiment.
Ces structures métalliques autoportantes peuvent être conçues sur mesure pour s’adapter parfaitement à votre espace et à vos besoins spécifiques. Elles sont particulièrement adaptées pour le stockage de produits légers ou pour créer des zones de préparation de commandes à plusieurs niveaux.
L’installation d’une mezzanine nécessite une étude approfondie de la structure du bâtiment et des flux logistiques. Il est crucial de prendre en compte les aspects suivants :
- La capacité de charge du sol et de la structure existante
- Les systèmes d’accès (escaliers, monte-charges) et de sécurité
- L’intégration avec les systèmes existants de manutention et de gestion des stocks
Conception ergonomique du rayonnage pour améliorer la productivité
Une fois le type de rayonnage choisi, l’ergonomie de votre installation devient un facteur clé pour optimiser la productivité de votre entrepôt. Une conception bien pensée peut réduire significativement les temps de déplacement, minimiser les risques d’erreurs et améliorer les conditions de travail de vos employés.
Analyse des flux de travail avec la méthode des 5S
La méthode des 5S, issue du Lean Management , est un outil puissant pour optimiser l’organisation de votre entrepôt. Elle se compose de cinq étapes : Seiri (trier), Seiton (ranger), Seiso (nettoyer), Seiketsu (standardiser) et Shitsuke (maintenir). Appliquée à la conception de votre rayonnage, cette méthode permet d’identifier les inefficacités et d’améliorer les flux de travail.
Commencez par analyser les mouvements de vos opérateurs et les flux de marchandises. Identifiez les zones à forte activité et celles qui sont sous-utilisées. Cette analyse vous permettra de concevoir un agencement qui minimise les déplacements inutiles et optimise l’utilisation de l’espace.
L’application rigoureuse de la méthode des 5S peut conduire à une augmentation de la productivité allant jusqu’à 30% dans certains entrepôts.
Dimensionnement optimal des allées selon les normes INRS
Le dimensionnement des allées est crucial pour assurer à la fois l’efficacité opérationnelle et la sécurité dans votre entrepôt. L’Institut National de Recherche et de Sécurité (INRS) fournit des recommandations précises sur les dimensions minimales à respecter. Ces normes prennent en compte les types d’engins de manutention utilisés et les caractéristiques des charges manipulées.
Pour les allées principales, où circulent des chariots élévateurs, une largeur minimale de 3,20 mètres est généralement recommandée. Pour les allées secondaires, où seuls des transpalettes circulent, une largeur de 1,80 mètre peut suffire. Cependant, ces dimensions doivent être ajustées en fonction de vos équipements spécifiques et de la nature de vos opérations.
N’oubliez pas que des allées trop étroites peuvent ralentir les opérations et augmenter les risques d’accidents, tandis que des allées trop larges gaspillent de l’espace précieux. L’objectif est de trouver le juste équilibre entre efficacité et sécurité.
Systèmes de picking assisté : voice picking et pick-to-light
Les technologies de picking assisté peuvent considérablement améliorer l’efficacité et la précision des opérations de préparation de commandes. Deux systèmes se distinguent particulièrement : le voice picking et le pick-to-light .
Le voice picking utilise la reconnaissance vocale pour guider les opérateurs dans leurs tâches. Les instructions sont transmises via un casque, laissant les mains libres pour manipuler les produits. Ce système réduit les erreurs de picking et améliore la productivité en éliminant le besoin de lire des listes papier ou des écrans.
Le pick-to-light, quant à lui, utilise des signaux lumineux pour indiquer les emplacements et les quantités à prélever. Des afficheurs LED installés sur les rayonnages s’allument pour guider l’opérateur vers les bons emplacements. Ce système est particulièrement efficace pour les opérations à haute cadence impliquant un grand nombre de références.
L’intégration de ces technologies dans votre conception de rayonnage peut améliorer significativement la productivité et la précision de vos opérations de picking. Ces systèmes peuvent réduire les erreurs de picking de plus de 50% tout en augmentant la productivité de 20 à 40%.
Sécurité et conformité des installations de rayonnage
La sécurité est un aspect fondamental dans la conception et l’utilisation des systèmes de rayonnage industriel. Non seulement elle protège vos employés et vos marchandises, mais elle est également une obligation légale.
Réglementation française NF EN 15635 sur l’inspection des rayonnages
La norme NF EN 15635 établit les lignes directrices pour l’inspection, la maintenance et la réparation des rayonnages métalliques. Elle impose des contrôles réguliers pour garantir la sécurité et la pérennité des installations. Selon cette norme, trois types d’inspections sont nécessaires :
- Inspection visuelle quotidienne par les opérateurs
- Inspection hebdomadaire par le responsable de l’entrepôt
- Inspection annuelle par un expert qualifié
Ces inspections doivent être documentées et les problèmes identifiés doivent être corrigés rapidement. La non-conformité à cette norme peut entraîner des sanctions légales et compromettre la sécurité de votre entrepôt.
Dispositifs anti-chute et protection des montants
Pour prévenir les accidents liés aux chutes de marchandises ou aux collisions avec les rayonnages, plusieurs dispositifs de sécurité sont essentiels :
- Grilles anti-chute : installées à l’arrière des rayonnages pour empêcher la chute de produits
- Protections de pieds de montants : pour absorber les chocs des chariots élévateurs
- Butées de palettes : pour éviter que les palettes ne soient poussées trop loin
Ces dispositifs, bien que simples, peuvent considérablement réduire les risques d’accidents et de dommages matériels. Leur installation doit être prévue dès la conception de votre système de rayonnage.
Formation du personnel à la manutention sécurisée
La sécurité dans un entrepôt dépend en grande partie des pratiques de travail des employés. Une formation approfondie et régulière du personnel est donc cruciale. Cette formation doit couvrir :
- Les techniques de manutention manuelle sécurisée
- L’utilisation correcte des équipements de protection individuelle
- Les procédures d’urgence en cas d’accident
- L’identification et le signalement des dangers potentiels
Investir dans la formation de votre personnel non seulement améliore la sécurité, mais contribue également à une utilisation plus efficace et durable de vos installations de rayonnage.
Optimisation du rayonnage avec les technologies d’automatisation
L’automatisation révolutionne la gestion des entrepôts, offrant des opportunités sans précédent pour optimiser l’utilisation des rayonnages et améliorer l’efficacité globale des opérations. Examinons les technologies clés qui transforment les entrepôts modernes.
Systèmes de stockage automatisés AS/RS
Les systèmes de stockage et de récupération automatisés (AS/RS) représentent une avancée majeure dans l’optimisation de l’espace de stockage. Ces systèmes utilisent des transstockeurs ou des navettes pour déplacer automatiquement les palettes ou les bacs dans des rayonnages à grande hauteur, pouvant atteindre 30 mètres ou plus.
Les avantages des systèmes AS/RS sont nombreux :
- Utilisation maximale de la hauteur disponible
- Réduction significative de l’empreinte au sol
- Amélioration de la précision et de la rapidité des opérations
- Réduction des erreurs humaines et des dommages aux produits
Bien que l’investissement initial soit conséquent, les AS/RS peuvent offrir un retour sur investissement rapide pour les entreprises gérant de grands volumes de stock avec des mouvements fréquents.
AGV et robots de manutention pour la gestion des stocks
Les véhicules à guidage automatique (AGV) et les robots de manutention transforment la façon dont les marchandises sont déplacées dans l’entrepôt. Ces machines autonomes peuvent naviguer dans les allées, prélever et déposer des palettes ou des bacs, et même effectuer des opérations de picking.
L’intégration d’AGV et de robots dans votre système de rayonnage peut améliorer considérablement l’efficacité de vos opérations. Ces technologies permettent :
- Une utilisation optimale de l’espace, les AGV pouvant opérer dans des allées plus étroites
- Une réduction des erreurs de picking et de placement
- Un fonctionnement 24/7, augmentant la productivité globale
- Une meilleure traçabilité des mouvements de stock
Pour tirer le meilleur parti de ces technologies, il est essentiel de repenser la conception de vos rayonnages pour faciliter l’accès et les mouvements des robots.
WMS intégré pour une allocation dynamique des emplacements
Un système de gestion d’entrepôt (WMS) avancé est le cerveau qui optimise l’utilisation de vos rayonnages. Grâce à l’allocation dynamique des emplacements, le WMS peut continuellement optimiser le placement des produits en fonction de multiples critères :
- La fréquence de picking
- Les caractéristiques physiques des produits
- Les contraintes de stockage (température, fragilité, etc.)
- Les prévisions de demande
Cette approche dynamique permet une utilisation plus efficace de l’espace de stockage, réduisant les déplacements inutiles et améliorant la productivité globale. De plus, un WMS intégré peut s’interfacer avec les systèmes AS/RS et les robots pour créer un écosystème d’entrepôt intelligent et hautement efficace.
Maintenance préventive et gestion de la durée de vie du rayonnage
Un système de rayonnage bien entretenu est essentiel pour la sécurité et l’efficacité de votre entrepôt. La maintenance préventive permet non seulement d’éviter les pannes et les accidents, mais aussi de prolonger la durée de vie de vos installations. Examinons les meilleures pratiques pour maintenir vos rayonnages en excellent état.
Planification des inspections selon la norme FEM 9.851
La Fédération Européenne de la Manutention (FEM) a établi des lignes directrices pour l’inspection et la maintenance des systèmes de rayonnage. La norme FEM 9.851 recommande un programme d’inspection rigoureux :
- Inspections visuelles quotidiennes par les opérateurs
- Inspections hebdomadaires par les superviseurs
- Inspections trimestrielles approfondies par du personnel qualifié
- Inspections annuelles par des experts externes
Ces inspections régulières permettent de détecter rapidement les problèmes potentiels tels que les déformations, les dommages dus aux impacts, ou les fixations desserrées. En suivant ce programme, vous pouvez prévenir les défaillances majeures et assurer la longévité de vos rayonnages.
Techniques de réparation in-situ des rayonnages endommagés
Lorsque des dommages mineurs sont détectés, il est souvent possible de les réparer sans démonter entièrement le rayonnage. Les techniques de réparation in-situ peuvent inclure :
- Le remplacement de composants endommagés (montants, traverses, etc.)
- Le renforcement des zones affaiblies
- La réalignement des structures déformées
Il est crucial que ces réparations soient effectuées par du personnel qualifié et conformément aux spécifications du fabricant. Une réparation mal exécutée peut compromettre l’intégrité structurelle du rayonnage et créer des risques de sécurité.
Analyse coût-bénéfice du remplacement vs réparation
La décision de réparer ou de remplacer un système de rayonnage endommagé doit être basée sur une analyse coût-bénéfice approfondie. Considérez les facteurs suivants :
- Le coût de la réparation par rapport au coût du remplacement
- L’âge et l’état général du système de rayonnage
- L’impact sur les opérations pendant la réparation ou le remplacement
- Les améliorations potentielles offertes par un nouveau système
Dans certains cas, le remplacement peut offrir des avantages à long terme en termes d’efficacité et de sécurité, justifiant l’investissement initial plus élevé. Consultez des experts en rayonnage industriel pour obtenir une évaluation précise de votre situation.